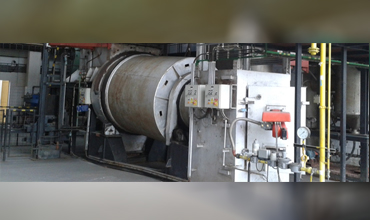
Destruction of hazardous compounds present in the waste by means of thermal destruction/oxidation followed by treatment of off gasses before letting them into atmosphere. The Incineration system design is done based on type/nature/characteristics of wastes. We have enough experienced & capable to design, engineering, manufacture & supply of Incineration System for Hazardous wastes from various industries and Biomedical Wastes.
Our design of Incinerator is custom built with the following major equipment:
- Primary Chamber with options of Stationary / Rotary Kiln / Spray Chamber / Pyrolysis Chamber based on waste nature.
- Secondary Combustion Chamber.
- Air Pollution Control Equipment for flue gas treatment.
- Stack of 30 meters height as per PCB guidelines.
We are capable to design Incineration System suitable to handle the following type of wastes:
- Industrial Hazardous Waste
- Liquid (Organic & Aqueous)
- Solid, Semisolid, Tarry Wastes
- Gaseous/VOC/Fumes
- Hospital/Biomedical Wastes
- Trash/Garbage/Canteen Wastes
Following are the types of Incineration Systems can be offered based on nature of wastes:
Stationary Type Incineration Systems : Stationary Type Incineration System is suited for organic liquids, gaseous and solid wastes with low ash content, capacity in the range of 100-150 Kg/Hr. This type of Incinerator is not suitable for wastes with higher % of ash content as they need continuous discharge. This type Incineration system is easy for operation & economical.
Rotary Kiln type Incineration System : Best Suited for any kind of wastes. Quite common system used all over the world. Suitable for even waste of smaller feed rate 100 Kgs/hr. to even tons/hour. Versatile for all types of wastes. Best suited for large / unknown characteristics of wastes. Best suited for wastes containing higher ash contents as ash can be discharged continuously. Economical Operation.
Pyrolysis type Incineration System : Specially designed for Organic tarry wastes which are sticky in nature, containing more organics/VOCs & lesser % of ash content. Mostly used for disposal of drummed wastes. Minimised material handling. Thermal Oxidiser : Mainly designed for gaseous wastes high in volume & low % of Organics/VOC. There are two types of Thermal Oxidiser i.e. Regenerative & Recuperative. These are most effective & economical methods used for destruction of VOC laden gaseous wastes.
1. Regenerative Thermal Oxidiser uses the Ceramic media to recover the heat from flue gases with heat recovery efficiency up to 95%. Best suited for large volume with lean VOCs gaseous wastes. There are no ash/effluent generation from the system. Easy to operate & maintain, low Operation cost with high capital investment.
2. Recuperative Thermal Oxidiser uses heat exchanger to recover the heat from flue gases by preheating of gaseous wastes & hot air for curing/drying chambers. Specially developed for colour/chemical coating application. There are no ash/effluent generation from the system. Easy to operate & maintain, low Operation cost.
Spray Incineration : Spray Incineration System designed to handle Liquid Organic & Aqueous wastes with more inorganics/salt content.
Biomedical/Hospital/Garbage : Biomedical/Hospital/Garbage waste Incineration system designed handle all types of hospital/pathological/garbage wastes with higher level of moisture content. Specially designed for optimum fuel economy & meet the PCB guidelines.
Air Pollution Control (APC) : Air Pollution Control (APC) Equipment are designed carefully with best available technology to meet the emission levels as laid down by pollution control board. Special attention given while designing the APC system to avoid any liquid/effluent generation – adopted the Zero Liquid Discharge concept.
Control & Automation : Control & Automation – adequate instruments & controls, safety interlocks would be provided with the system for easy & safe operation. We can offer fully mechanized, automated, PLC based system on need basis including continuous emission monitoring system.